広幅コーティング後のスリット加工による加工時間の短縮(コストダウン事例)
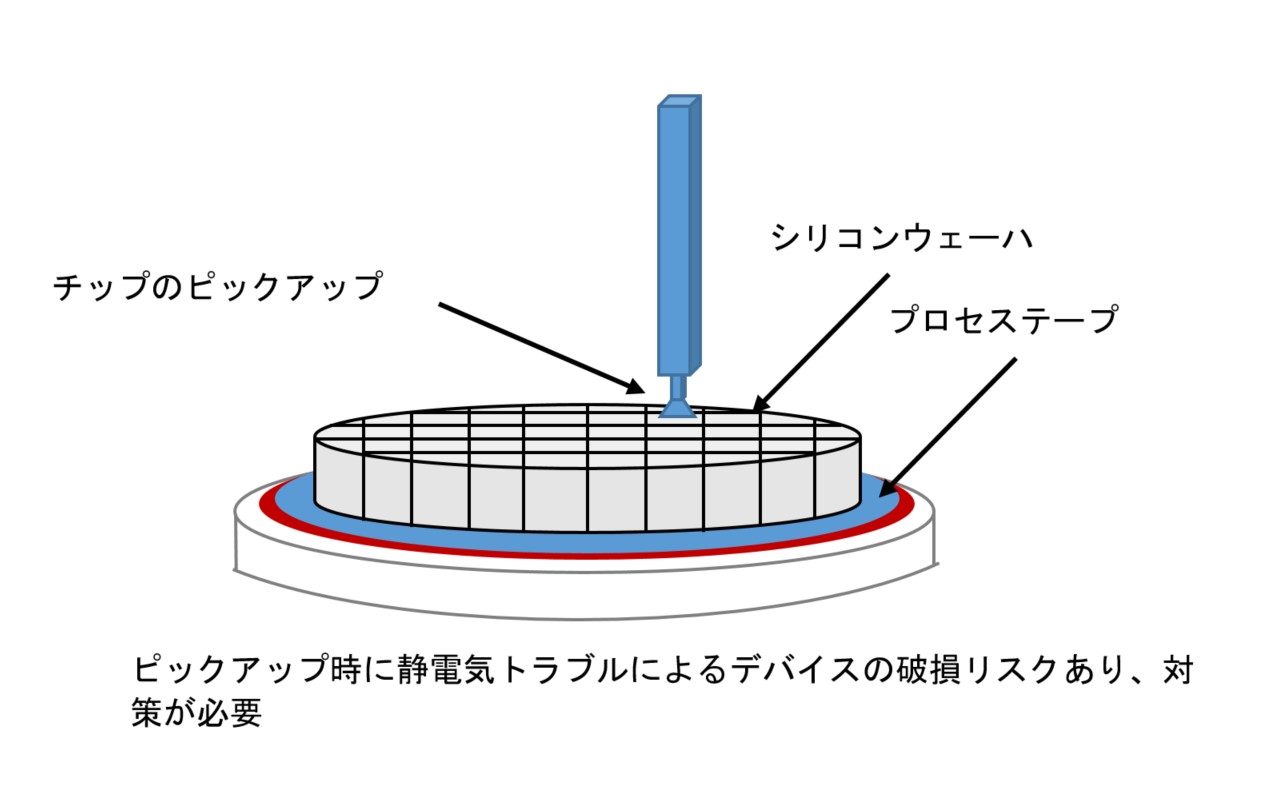
提案業界 | テープメーカー |
---|---|
トラブル内容 | 静電気発生・コストが高い |
対象物 | 半導体プロセステープ |
お客様の課題・お困りごと
加工プロセスの都合で、特性のある軟質基材を使用しなければいけないが、基材の帯電量が大きく、チップをピックアップする際に帯電した静電気が悪影響して、ピックアップを失敗するケースが発生してしまい、歩留まりが悪いことが課題でした。
また、基材の帯電防止グレードが無く、別途行うにしても予算が厳しい状況でコストダウンが必要でした。
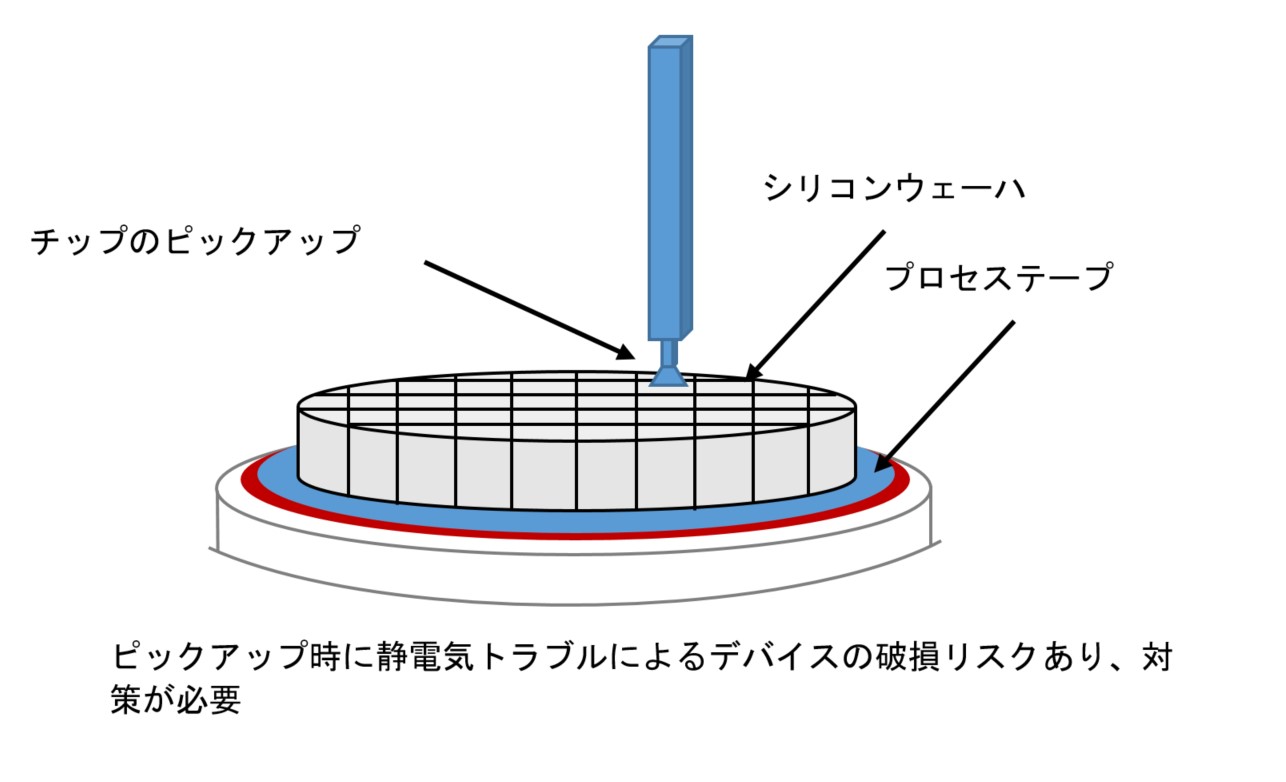
当社のご提案内容
当社からは、コーティング工程の加工時間削減によるコストダウンをご提案いたしました。
最終製品幅400㎜の基材に対して帯電防止処理を行うとコストが一気に跳ね上がり予算を超えてしまうため、
当社の特殊広幅コーターにて、広幅(1250㎜)で帯電防止処理を行った後、
400㎜に3丁スリットを行ことで、お客様要望の帯電防止処理の機能を付与しつつ、
生産効率を上げることで、生産コストを抑え、限られた予算の中で製品を設計が可能になりました。
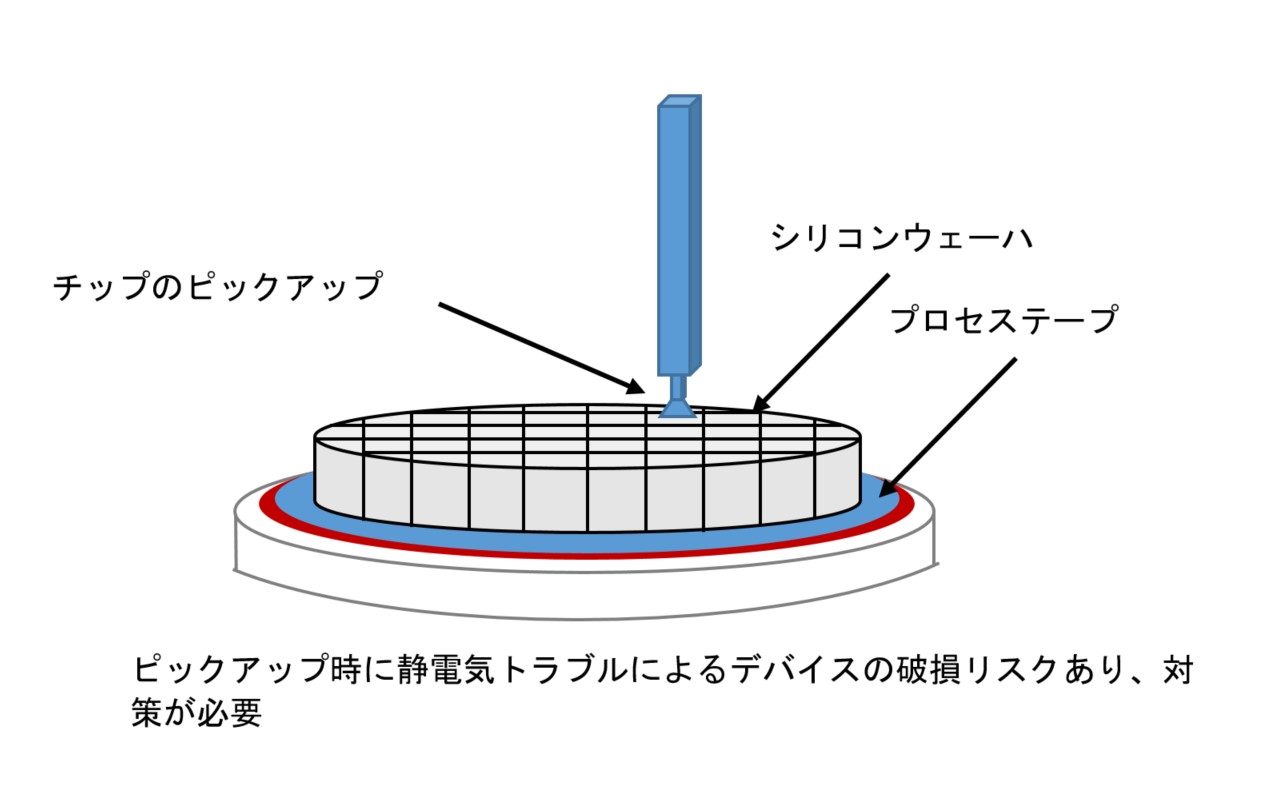
提案ポイントとお客様のご感想
要望の帯電防止処理性能が付与されたことで、プロセス中の静電気トラブルが解決したことに加え、
限られた予算内での生産が実現できたため、お客様の新規案件受注に寄与することができました。
当社の帯電防止フィルムは、コーティング技術を活用して帯電防止剤を塗布することで機能性をふかしています。
練りこみの帯電防止フィルムと比較して、塗布型の帯電防止フィルムは基材を選ばず、任意の基材に帯電防止性を付加することが可能です。
また、帯電防止性能に即効性があるのに加え、効果の持続が長いことも特長です。
塗布型は量産の場合、練りこみ型より高価ですが、広幅コーターによる加工とスリットにより、
加工時間を削減し、量産においても当事例のようにコストアップを最小限に抑えることが可能です。
要望の帯電防止性とコストダウンの両立にお困りの方は当社までお問い合わせください。
>>当社の取り扱う帯電防止フィルムについてはこちら